What Is Lean?
Discover the power of Lean principles! Uncover the origins, techniques, and benefits of this game-changing methodology.
.jpg)
Introduction to Lean Principles
To improve the efficiency and effectiveness of businesses, many organizations are embracing the principles of Lean. This management philosophy, originating from the manufacturing industry, has now found applications across various sectors. By understanding the fundamental concepts and techniques of Lean, businesses can streamline their processes and achieve better outcomes.
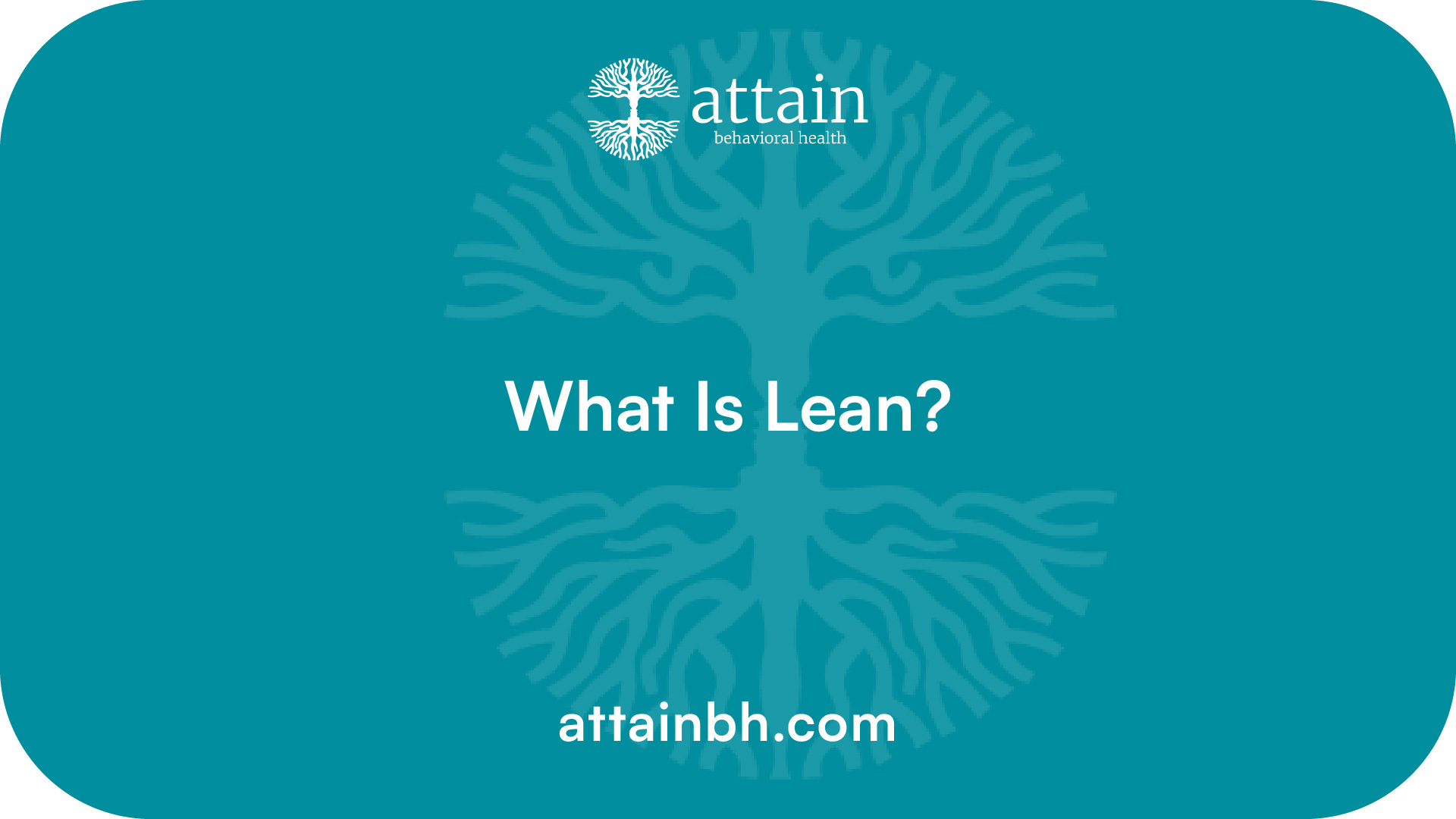
What is Lean?
Lean is an approach that focuses on maximizing value for customers while minimizing waste. It emphasizes the continuous improvement of processes, elimination of non-value-added activities, and the respect for people within the organization. At its core, Lean aims to create a culture of effectiveness, efficiency, and continuous learning.
Origins of Lean Thinking
The roots of Lean can be traced back to the Toyota Production System (TPS), which was developed by Toyota in Japan. The TPS revolutionized the manufacturing industry by introducing concepts such as just-in-time production and the elimination of waste. Taiichi Ohno, an engineer at Toyota, played a pivotal role in developing and implementing these principles.
The success of the TPS and its ability to deliver high-quality products at a faster pace with lower costs caught the attention of businesses worldwide. As a result, Lean principles were adopted and adapted by organizations in various industries beyond manufacturing, including healthcare, software development, and more.
By embracing Lean, businesses can improve their operational efficiency, reduce costs, and enhance the quality of their products or services. In the following sections, we will explore the core concepts, techniques, benefits, and challenges of implementing Lean in different industries.
Core Concepts of Lean
To truly embrace the principles of Lean, it's essential to understand its core concepts. These concepts form the foundation of Lean thinking and guide organizations towards achieving operational excellence. The three key core concepts of Lean are continuous improvement, elimination of waste, and respect for people.
Continuous Improvement
Continuous improvement, also known as Kaizen, is a fundamental principle of Lean. It emphasizes the never-ending pursuit of excellence and the belief that there is always room for improvement. By fostering a culture of continuous improvement, organizations can identify and address inefficiencies, bottlenecks, and other areas of improvement on an ongoing basis.
The philosophy of continuous improvement encourages employees at all levels to contribute their ideas and suggestions for process enhancement. Through regular feedback, data analysis, and problem-solving techniques, organizations can make incremental changes that lead to significant improvements over time.
Elimination of Waste
One of the primary goals of Lean is to eliminate waste in all its forms. Waste refers to any activity, process, or resource that does not add value to the customer. By identifying and eliminating waste, organizations can streamline their operations, improve efficiency, and maximize customer satisfaction.
There are several types of waste that Lean focuses on, including:
- Transportation: Unnecessary movement of materials or products.
- Inventory: Excess inventory that ties up resources and increases costs.
- Motion: Unnecessary movement of people or equipment.
- Waiting: Idle time caused by delays in the production process.
- Overproduction: Producing more than what is required by the customer.
- Overprocessing: Performing unnecessary steps or activities that do not add value.
- Defects: Errors or defects that require rework or lead to customer dissatisfaction.
By identifying and eliminating these forms of waste, organizations can optimize their processes, reduce costs, and deliver products or services more efficiently.
Respect for People
In the Lean philosophy, respect for people is a fundamental principle that emphasizes the value of every individual in the organization. This principle recognizes that the success of Lean initiatives depends on the involvement, engagement, and empowerment of employees at all levels.
Respect for people involves creating a work environment that fosters collaboration, open communication, and mutual respect. It encourages organizations to value the knowledge, skills, and expertise of their employees and actively involve them in decision-making processes. By empowering employees, organizations can tap into their creativity, problem-solving abilities, and commitment to drive continuous improvement.
Additionally, respect for people includes providing training and development opportunities, ensuring a safe and healthy work environment, and recognizing and rewarding employees for their contributions. When people feel respected and valued, they are more likely to be motivated, engaged, and committed to the success of Lean initiatives.
By embracing continuous improvement, eliminating waste, and promoting respect for people, organizations can unlock the true potential of Lean and achieve sustainable success in their pursuit of operational excellence.
Lean Techniques and Tools
To effectively implement lean principles and achieve process improvement, various techniques and tools are utilized. These tools aid in identifying and eliminating waste, streamlining processes, and fostering a culture of continuous improvement. In this section, we will explore three essential lean techniques and tools: value stream mapping, 5S methodology, and kaizen.
Value Stream Mapping
Value stream mapping is a visual representation technique that enables organizations to analyze and understand the flow of materials and information required to deliver a product or service. It provides a comprehensive view of the entire process, including both value-added and non-value-added activities.
By mapping out the current state of the value stream, organizations can identify areas of waste, bottlenecks, and inefficiencies. This understanding allows them to develop a future state map, envisioning a more streamlined and efficient process. Value stream mapping is a collaborative effort involving stakeholders from different departments, fostering cross-functional communication and shared understanding.
The following table provides an overview of the key steps involved in value stream mapping:
Steps in Value Stream Mapping
- Identify the product or service
- Map the current state value stream
- Analyze and identify areas of waste
- Develop the future state value stream
- Implement improvements
- Continuously monitor and refine the value stream
5S Methodology
The 5S methodology is a systematic approach to workplace organization and standardization. It aims to create a clean, efficient, and safe work environment by eliminating clutter, optimizing workflow, and promoting visual management.
The 5S method consists of the following steps:
Steps in the 5S Methodology
- Sort: Remove unnecessary items from the workspace
- Set in Order: Organize and arrange necessary items for easy accessibility
- Shine: Clean and maintain the workplace
- Standardize: Establish standardized work procedures and visual cues
- Sustain: Continuously practice and improve the 5S system
Implementing the 5S methodology helps reduce wasted time searching for tools and materials, improves safety, and fosters a sense of ownership and pride in the workplace.
Kaizen
Kaizen, which means "continuous improvement" in Japanese, is a core principle of lean thinking. It emphasizes the importance of making small, incremental changes to processes on an ongoing basis. Kaizen encourages employees at all levels to contribute ideas and suggestions for improvement, promoting a culture of innovation and engagement.
The key steps in the kaizen process include:
Steps in the Kaizen Process
- Identify areas for improvement
- Gather and analyze data
- Develop and implement improvement ideas
- Monitor and evaluate the results
- Standardize and sustain the improvements
Kaizen encourages organizations to continually seek opportunities for improvement, no matter how small. By embracing a kaizen mindset, organizations can achieve significant long-term improvements in efficiency, quality, and customer satisfaction.
By leveraging these lean techniques and tools, organizations can optimize processes, reduce waste, and drive continuous improvement. Value stream mapping provides a holistic view of the process, while the 5S methodology ensures a clean and organized work environment. Lastly, kaizen cultivates a culture of ongoing improvement, empowering employees to contribute to the organization's success.
Benefits of Implementing Lean
Implementing Lean principles in a business can bring about a multitude of benefits, positively impacting various aspects of the organization. Let's explore three key advantages of embracing Lean: increased efficiency, cost reduction, and enhanced quality.
Increased Efficiency
One of the primary goals of Lean is to streamline processes and eliminate wasteful activities, ultimately leading to increased efficiency. By identifying and eliminating non-value adding steps, businesses can optimize their operations and minimize unnecessary tasks or delays.
Through Lean techniques such as value stream mapping and the 5S methodology, organizations gain a deeper understanding of their workflows and can identify areas for improvement. By implementing changes based on these insights, businesses can minimize bottlenecks, reduce cycle times, and enhance overall productivity.
Cost Reduction
Lean principles also contribute to significant cost reduction within an organization. By eliminating waste and improving efficiency, businesses can reduce expenses associated with excess inventory, overproduction, waiting times, and inefficient resource utilization.
Additionally, Lean encourages a culture of continuous improvement and empowers employees to identify cost-saving opportunities. When team members are engaged in Lean practices, they become more attuned to identifying and addressing areas of waste or inefficiency, leading to ongoing cost savings.
Enhanced Quality
Quality is a vital aspect of any business, and Lean principles can greatly contribute to its enhancement. By focusing on the elimination of waste and the standardization of processes, Lean helps to identify and address quality issues at their root cause.
Through Lean techniques like Kaizen, which emphasizes continuous improvement, organizations promote a culture of quality-consciousness. This results in improved product or service quality, reduced defects, and enhanced customer satisfaction.
By implementing Lean practices, businesses can achieve a higher level of operational excellence, leading to increased efficiency, cost reduction, and enhanced quality. However, it's important to note that successful implementation of Lean requires commitment, engagement, and ongoing effort from all levels of the organization.
By embracing Lean principles, businesses can unlock these benefits and create a foundation for long-term success in today's competitive landscape.
Applying Lean in Different Industries
The principles of Lean can be applied across various industries to improve efficiency, reduce waste, and enhance overall performance. Let's explore how Lean is implemented in three different sectors: manufacturing, healthcare, and software development.
Manufacturing
In the manufacturing industry, Lean principles have been widely adopted to streamline processes, increase productivity, and optimize resource utilization. By implementing Lean techniques, manufacturers aim to eliminate waste, improve quality, and deliver products more efficiently.
One of the core Lean methodologies used in manufacturing is the Toyota Production System (TPS), which focuses on continuous improvement and waste reduction. Lean manufacturing techniques such as Just-in-Time (JIT) production, Kanban systems, and cellular manufacturing help minimize inventory, reduce lead times, and enhance overall workflow.
By implementing Lean in manufacturing, companies can achieve significant benefits, including improved production efficiency, reduced costs, and enhanced product quality. The table below highlights some of the advantages of Lean implementation in the manufacturing industry:
Benefits of Implementing Lean in Manufacturing
- Increased Production Efficiency
- Reduced Costs and Waste
- Enhanced Product Quality
- Improved Lead Times
- Streamlined Workflow
Healthcare
Lean principles are also gaining traction in the healthcare industry, where the focus is on improving patient care, reducing errors, and enhancing operational efficiency. Lean methodologies are applied to streamline processes, eliminate waste, and create a culture of continuous improvement within healthcare organizations.
Value Stream Mapping (VSM) is a Lean technique commonly used in healthcare to visualize the patient journey and identify areas of improvement. By mapping out the value stream, healthcare providers can identify bottlenecks, reduce wait times, and enhance the overall patient experience.
In addition to VSM, Lean healthcare also incorporates concepts such as 5S methodology, which focuses on organizing the workplace for efficiency, and Kaizen, which encourages small, incremental improvements. These Lean tools help healthcare organizations optimize their processes, improve patient outcomes, and reduce costs.
Implementing Lean in healthcare can result in numerous benefits, including improved patient satisfaction, reduced medical errors, and enhanced resource utilization. The table below outlines some of the advantages of Lean implementation in the healthcare industry:
Benefits of Implementing Lean in Healthcare
- Enhanced Patient Satisfaction
- Reduced Medical Errors
- Improved Resource Utilization
- Streamlined Workflows
- Increased Operational Efficiency
Software Development
Lean principles can also be applied to software development, enabling teams to deliver high-quality software products more efficiently. Lean software development focuses on minimizing waste, improving collaboration, and continuously delivering customer value.
One of the key principles of Lean software development is the concept of delivering in small, frequent increments. This approach, known as Agile development, allows software teams to gather feedback early and make necessary adjustments throughout the development process.
Lean software development also emphasizes the importance of cross-functional teams, encouraging collaboration and knowledge sharing among team members. This enables faster decision-making and reduces delays in project delivery.
By implementing Lean in software development, organizations can achieve benefits such as faster time-to-market, improved product quality, and increased customer satisfaction. The table below highlights some of the advantages of Lean implementation in the software development industry:
Benefits of Implementing Lean in Software Development
- Faster Time-to-Market
- Improved Product Quality
- Enhanced Customer Satisfaction
- Increased Collaboration and Efficiency
- Reduced Waste and Rework
Applying Lean principles across various industries allows organizations to optimize their processes, reduce waste, and improve overall performance. By embracing Lean methodologies, manufacturing, healthcare, and software development sectors can achieve tangible benefits and drive continuous improvement.
Challenges of Implementing Lean
Implementing Lean principles within an organization can bring about numerous benefits, but it is not without its challenges. Overcoming these challenges is essential to ensure a successful Lean transformation. Let's explore some common hurdles faced during the implementation process.
Resistance to Change
One of the primary challenges of implementing Lean is resistance to change. People are often resistant to new processes and ways of working, especially if they have been accustomed to the existing practices for a long time. It is crucial to address this resistance and create a culture of openness to change.
To overcome resistance, organizations should focus on effective communication and education. Providing clear explanations about the purpose and benefits of Lean can help individuals understand the need for change. Involving employees in the decision-making process and encouraging their input can also foster a sense of ownership and engagement.
Lack of Leadership Support
Another challenge is the lack of support from leadership. When leaders do not fully embrace and champion Lean principles, it becomes difficult to drive the necessary changes throughout the organization. Leadership commitment and involvement are vital for the successful implementation of Lean.
To address this challenge, it is crucial to emphasize the importance of leadership buy-in. Leaders need to understand the value of Lean and how it can positively impact the organization. Providing training and education to leaders, highlighting successful Lean implementations in other companies, and demonstrating the potential benefits can help in gaining their support.
Overcoming Implementation Hurdles
Implementing Lean can encounter various hurdles unique to each organization. Some common implementation hurdles include inadequate resources, lack of employee engagement, and resistance from middle management. Overcoming these hurdles requires a strategic and flexible approach.
Organizations should prioritize providing the necessary resources, including training, tools, and time, to support Lean implementation. Engaging employees at all levels and involving them in problem-solving and process improvement activities can increase their commitment and motivation. Addressing resistance from middle management by involving them in the Lean journey and helping them understand the benefits can also contribute to a smoother implementation.
By recognizing and addressing these challenges head-on, organizations can navigate the implementation process more effectively and increase the likelihood of achieving the desired outcomes of Lean. It is important to remember that Lean is a continuous improvement journey, and challenges may arise along the way. With perseverance, dedication, and a focus on problem-solving, organizations can successfully implement Lean and reap the benefits it offers.
Sources
https://www.wavesofhopeed.com/what-is-lean
https://www.healthline.com/health/what-is-lean
https://www.medicalnewstoday.com/what-is-lean
https://www.justthinktwice.gov/what-lean
https://www.ashleytreatment.org/rehab/what-is-lean
Similar articles
Start Your Recovery Today!
Build a foundation for lasting recovery.